Tabletop Conveyors
Intermediate Sections
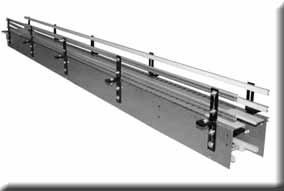
An intermediate section is the section of the conveyor that transports the product between the drive and idle end.
- 5 1/2” deep frame
- UHMW clip on wearstrip
- Adjustable guide rail
Curves
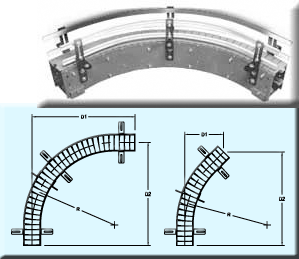
A curve is used to change conveyor direction with a continuous motion, utilizing side flexing chain. This direction change occurs without the use of a deadplate or an additional drive.
- Lubricated UHMW inside wearstrips
- Option for Nylatron wearstrip (Recommended for speeds above 128 fpm)
- 5 1/2” deep frame
- Radius is measured to centerline of chain (inside chain on dual wide)
- 0’ – 6” striaght at each end
Idle End Assemblies
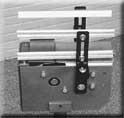
The idle end assembly is the beginning point of the conveyor where the return chain is now the carrying chain.
- 3’ – 0” O.A.L. with standard below motor mount
- 8” deep frame
- Finger guard included.
Motor/reducer sold separately.
Drive End Assemblies
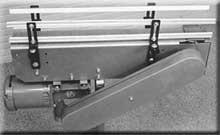
The drive end is the ending point of the conveyor where the motor is located. The product carrying chain becomes the return chain.
- Lubricated UHMW inside wearstrips
- Option for Nylatron wearstrip (Recommended for speeds above 128 fpm)
- 5 1/2” deep frame
- Radius is measured to centerline of chain (inside chain on dual wide)
- 0’ – 6” striaght at each end.
Deadplate Turns
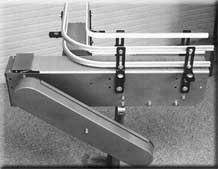
A deadplate turn is used to change conveyor direction by 90 degrees utilizing straight running chain. This type of direction change requires the use of a deadplate and an additional drive. Speed changes can be made at this point. Back pressure is required to make the transfer across the deadplate.
- 3’-0” x 1’-0” O.A.L. with standard below motor mount (325, 450, 750)
- 4’-0” x 1’-0” O.A.L. with standard below motor mount (1500)
- 8” deep frame
- Adjustable stainless steel deadplate
Parallel Transfers
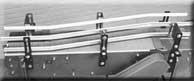
A parallel transfer is used when you need to end one chain pull and begin another. This transfer insures a smooth product transition by moving the product from one chain to the other, without the use of a deadplate. A parallel transfer may be used when the size of the product will not allow for an end to end transfer or to break up line back pressure for better line control. If product spacing is a concern, a parallel transfer may be used by incorporating a speed change between the infeed and discharge chains.
- 4’ – 0” O.A.L. with standard below motor mount (325, 450, 750)
- 5’-0” O.A.L. with standard below motor mount (1500)
- Minimum 1/16” gap between chains
- 8” deep frame